Laser scanners are regarded as safe, reliable, and modern, simply an ideal protective measure. Where is the catch?
Safety scanners are protective devices designed to detect the approach or presence of potentially endangered individuals. The official[1]according to EN IEC 61496-3:2019 Safety of machinery. Electro-sensitive protective equipment. Part 3. Particular requirements for active opto-electronic protective devices responsive to diffuse … Continue reading name for this group of devices is so complex (active opto-electronic protective devices responsive to diffuse reflection) that its acronym (AOPDDR) is nearly as long as the word „scanner” itself — let’s stick with the customary name, therefore.
operating principle
Scanner operates on the principle of radar, with all the inherent limitations. A laser beam (infrared radiation with a length of 820-946 nm[2]IEC 61496-3, 4.2.14 scans a segment of a circle (typically 180-270°), and a photosensitive element (located within the same housing) detects any reflections from objects within the monitored field.
The detection area of the scanner can be customized to a great extent. It can be shaped, for example, as a rectangle that covers the work area, and certain areas within it can be excluded, such as areas containing fixed elements like pillars or the machine’s body. The only limitation on the shape of the monitored area is the (obvious) principle that the laser beam can intersect the boundary of the area only once (or the boundary may run along the radius).
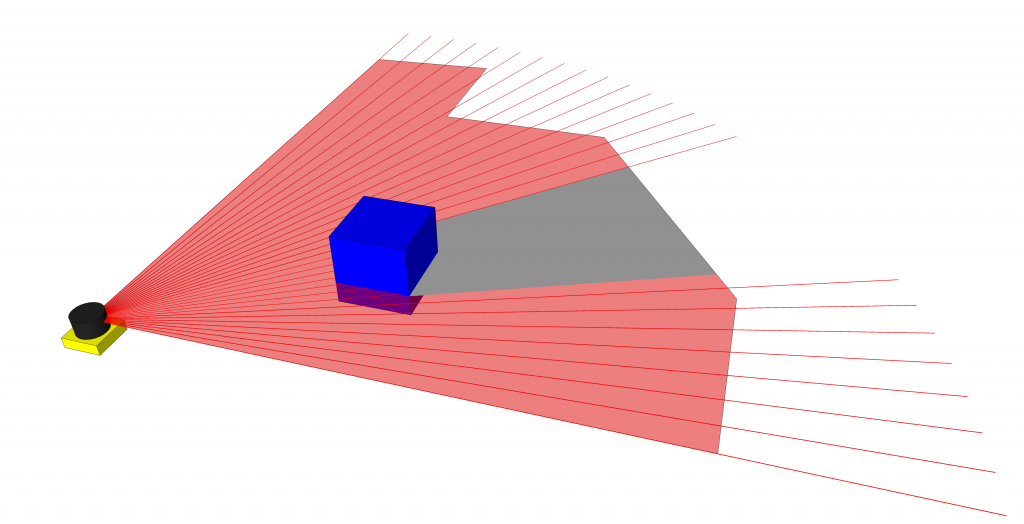
Integrating the transmitter and receiver in a single, compact housing allows for the use of scanners in places where installing a curtain is not practicable. For instance, two vertical scanners can be used to monitor a workstation from two adjacent sides without any corner element that would obstruct access (provided that the scanners can be mounted vertically).

Example of using two scanners in a vertical arrangement
limits
Scanners have a longer response time (several tens of milliseconds) compared to optical curtains (a few milliseconds). In a curtain, each beam has its own transmitter and receiver, and the delay is only due to electronic operations. In a scanner, however, there is a single laser that sequentially illuminates each area, and the delay is caused mainly by the scanning mechanism. If the scanner is only intended to protect the operator from unexpected machine activation, this is not a problem. However, if the machine needs to be stopped upon detecting an approaching operator, the increased delay will require an increase in the distance from the hazardous elements, as described further.
The operating principle of a scanner inherently makes it susceptible to mistakes. A dust particle, if it reflects the beam, will be recognized by the scanner in a same way as an operator’s leg, potentially causing the machine to stop. To avoid this, the scanner configuration can specify how many times a reflection must occur in the same spot to be considered a macroscopic object. However, this means repeating the detection cycle multiple times, resulting in an increased (several times) response time for the scanner. It is not possible to achieve immunity to dust by simply reducing the sensitivity of the scanner, as this could lead to overlooking large but dark objects.[3]A perfectly black object will not be detected by the scanner because it does not reflect light. Fortunately, true blackness is rare. This problem does not occur with optical curtains — in that case, an object must be large enough to block the entire beam of radiation (or a significant portion of it) so that the beam does not reach the receiver.
An important parameter of optoelectronic devices is their detection capability, which refers to the minimum size of an object that will be reliably recognized. Due to the construction of a scanner, this capability is directly proportional to the distance from the device. When installing a scanner, it is important to ensure that the required detection capability is not exceeded for the size of the monitored area. In traditional applications, such as a horizontally-mounted scanner monitoring the presence in a hazardous zone, the critical value is the detection of objects with a diameter of 70 mm (i. e. calf thickness). Typically, this value also determines the scanner’s range (the distance at which the detection capability is exactly 70 mm). However, if the scanner is to be used in a different way, the required detection capability may be, for example, 25mm, resulting in an almost threefold reduction in the scanner’s actual range. For comparison, in optical curtains, the beams are parallel, so the detection capability does not vary with the increase in distance between the transmitter and receiver.
Another limitation is the performance level.[4]as defined in ISO 13849-1 While typical curtains allow for achieving safety functions at PL e CAT 4, scanners can only reach up to PL d CAT 3. This excludes scanners from monitoring the most critical hazards.[5]Theoretically, achieving PL e is possible by using two scanners in parallel to monitor the same area.
An equally important and often overlooked parameter is the width of the so-called tolerance zone. Distance measurement (i.e., determining whether an object is within the protected zone or outside) is done with finite accuracy. One manufacturer declares a measurement uncertainty of up to 10 cm,[6]Omron OS32C scanner while for another, it is difficult to find any data on this matter. In practice, the measurement uncertainty may be smaller than declared, but it always exists. If the scanner is intended to monitor the presence of individuals in a room, a gap equal to at least the maximum measurement error must be left between, for example, walls and the scanner’s detection zone. Otherwise, the wall may occasionally cause a process stoppage because the scanner may consider it closer than it is. However, if the gap between the active scanner zone and the wall is greater than 70 mm, it is possible to be undetected in that area according to ISO 13855. Therefore, if the scanner is indeed meant to detect people present in a hazardous area, additional devices may be necessary to prevent staying within the tolerance zone, which is subject to the scanner’s uncertain operation. Surroundings that easily reflect light (e.g., stainless steel casing) may cause additional disturbances.
It is also important to remember that the edge of the recognition area is not visible. If process stoppage can result in losses, it is better to clearly mark the boundaries of the supervised area, for example, by painting them on the floor.
summary
Laser safety scanners are irreplaceable in many situations — but in all other cases, it is worth considering alternatives. Optical curtains — if their application is possible — will allow for better utilization of workspace and can provide a higher level of safety, both for the process and the worker.
Note: Distancing the scanners from hazards will be covered in the next technical issue (i. e. in ca. four weeks).
Photo by Helmut Gevert from FreeImages. Translated with vast help of Aria. Illustrated with SketchUp.
ten artykuł to tłumaczenie dwóch wcześniejszych:
https://ocenaryzyka.pl/2020/skanery-czesc-1-zasada-dzialania-i-co-z-tego-wynika/
https://ocenaryzyka.pl/2020/skanery-czesc-ii-ograniczenia/